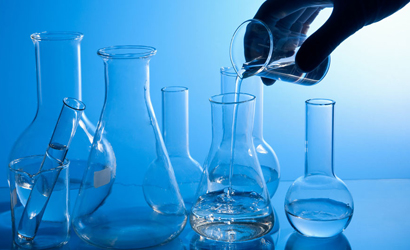
08 3月 硫化氢气体脱碳制备硫化钠方法

国内生产硫氢化钠常用硫化碱(钠 Na)吸收硫化氢的方法。而硫化钠的传统制备 方法有采用煤炭还原硫酸钠、硫化钡副产法,气体还原硫酸钠法,烧碱吸收硫化氢法等。目 前国内生产工业硫氢化钠的基本方法是用硫化钠溶液吸收硫化氢气体制造硫氢化钠。而国 内生产硫化钠基本上采用碳还原硫酸钠法,主要原料是芒硝和煤,工艺技术简单,但反应温 度高达 900 ~ 1100℃,因此煅烧煤还原芒硝生产硫化钠生产工艺存在高污染,高能耗等问 题。而且含铁、含碳酸钠盐是影响硫化钠产品质量的主要因素。利用含二氧化碳的硫化氢酸气制备硫氢化钠产品,是一种既可以净化气体,又可 以充分利用尾气中有价值成分的循环经济技术。
石化厂酸气主要组成是硫化氢,此外还含有部分二氧化碳,酸气制硫氢化钠或硫化钠是最经济的方法,但是二氧化碳存在干扰硫氢化钠或硫化钠的质量,因此脱碳成为必 要。国内酸气制硫氢化钠工艺仅有一套酸气脱碳装置,技术从日本引进,与两家日本厂家合 营,装置现设在山东东营的三协有限化学公司。该装置采用醇胺法脱碳,装置包括醇胺溶液 循环吸收和醇胺溶液循环再生两部分,醇胺溶液能吸收二氧化碳,也能吸收硫化氢,没有明 显的吸收选择性,因此溶剂再生时析出二氧化碳和硫化氢而成为二次污染源,解析气必须 进行脱硫处理才能排入环境。近年环保法规对尾气排放颁布严格的排放标准,部分炼油厂 将克劳斯尾气采用加氢处理,将二氧化硫气还原为硫化氢气,然后将还原气返回溶剂脱硫 装置。可见,醇胺法是传统的脱碳脱硫技术,对于同时存在硫化氢和二氧化碳的酸气场合, MDEA溶液不能清淅分离硫化氢和二氧化碳。炼油厂酸气加工制备硫氢化钠工艺碱洗涤吸收 硫化氢之前要求酸气脱除二氧化碳
二:操作方法
①缓冲溶液与未脱碳的硫化氢酸气进行混合反应吸收所述未脱碳的硫化氢酸 气中的二氧化碳和部分硫化氢,得到含有碳酸氢钠和硫氢化钠的脱碳富液; 所述缓冲溶液是含有氢氧化钠和碳酸氢钠的碱液 ;所述碱液中碳酸氢钠来自于氢 氧化钠对所述未脱碳的硫化氢酸气中的二氧化碳的吸收反应,所述碱液中氢氧化钠的质量 浓度为 10% ~ 40%,所述碱液的 pH 值为 8 ~ 12,所述混合反应的时间为 10 ~ 40 秒,所述混 合反应温度为50~100℃,所述碱液的循环量为所述未脱碳的硫化氢酸气中的二氧化碳质量的 30 ~ 100 倍 ;
②加热所述步骤①得到的脱碳富液,使脱碳富液中的硫氢化钠发生水解反应, 转化成氢氧化钠,并析放出硫化氢气体返回酸气系统 ;所述水解反应生成的氢氧化钠与所 述脱碳富液中的游离碱和碳酸氢钠反应生成碳酸钠 ;所述未脱碳的硫化氢酸气中的二氧化 碳最终生成碳酸钠盐被固定,得到脱除二氧化碳后的硫化氢酸气 ;而所述水解反应生成的 硫化氢最终被吸回酸气中,进入脱除硫化氢并制备硫氢化钠的单元操作 ;所述水解反应温 度 :70 ~ 100℃,所述水解反应压力 :-0.01 ~ -0.09MPa ;
③将所述步骤②得到的脱除二氧化碳后的硫化氢酸气进入管式混合反应器,用循环碱液逆向吸收得到含硫氢化钠的富液 ;该管式混合反应器依靠循环碱液的喷射产生吸 力将含硫化氢酸气吸入,采用气液逆向流动接触反应方式,连续加碱连续制备硫氢化钠,所 述循环碱液为含氢氧化钠的溶液,所述循环碱液的质量浓度为 30%~ 35%,所述气液逆向 流动接触反应的时间为 2 ~ 3 秒,所述气液逆向流动接触反应温度控制在 65 ~ 85℃内 ;
④将所述步骤③得到的含硫氢化钠的富液蒸发浓缩,制得不同品级的硫氢化钠产品,所述蒸发浓缩温度为 35 ~ 60℃,所述蒸发浓缩的压力为常压。
三:有益效果
本技术能有效地从硫化氢酸气中脱除二氧化碳,并且可以转化成有用产品碳 酸钠盐,脱碳率可以达到 60 ~ 90%。脱碳率高低的确定取决于酸气中二氧化碳含量和酸 气中硫化氢与二氧化碳的质量比例。脱碳工艺单元操作不产生二次污染源,并且得到产品。
*免责声明:本网站所载内容来源于互联网、微信公众号等公共渠道, 我们对文中观点保持中立态度。本文资讯仅供参考,交流之用。 本网站不对任何因使用所载内容所引致的损失承担任何风险及责任。转载的稿件版权归原著所有,如有侵权,请联系我们删除。